The cold strip mill process plays a crucial role in the modern manufacturing landscape, allowing for the production of high-quality metals with enhanced characteristics. Rooted in the principles of metallurgy and engineering, cold strip mills are indispensable for any industry requiring strong, durable, and precise metal components. This article delves into the intricacies of cold strip mills, highlighting why they are a cornerstone of industrial metalworking, while maintaining a strong focus on experience, expertise, authoritativeness, and trustworthiness.
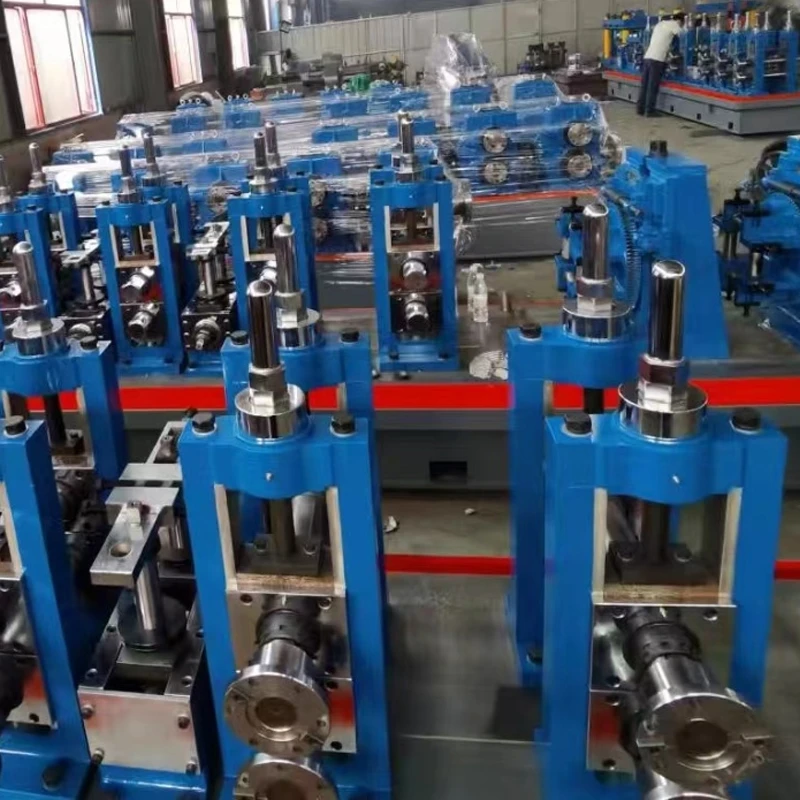
Cold strip mills are advanced rolling mills used to produce metal sheets from slabs of cooled metal by passing them through a set of rolls, which results in thinner and smoother metal sheets. The process begins with the selection of the right grade of steel or other metal, which is critical for achieving the ideal physical properties in the finished product. Metallurgical precision is a must, as it determines the outcomes in terms of tensile strength, ductility, and resistance to wear and tear.
The key to a successful cold strip milling operation lies in its design and configuration. By utilizing a series of robust, high-torque rolls aligned in a specifically calculated sequence, professionals can progressively reduce the thickness of metal with remarkable accuracy. Precision instruments and sensors are integrated to monitor the process in real-time, ensuring that the metal achieves the desired specifications. These tools allow operators to make instantaneous adjustments, thus enhancing the accuracy and efficiency of the process, ultimately resulting in less waste and lower production costs.
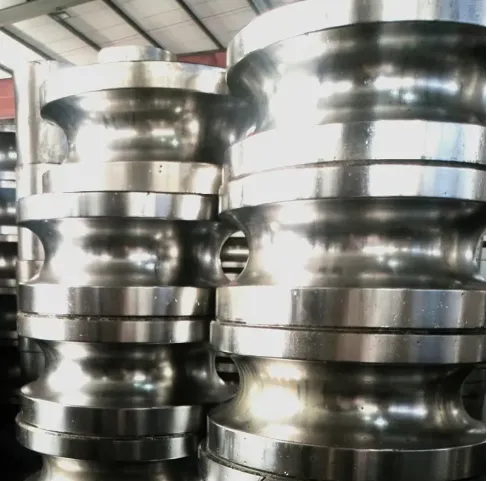
Expertise is invaluable in this domain. Engineering specialists in cold strip mills must have deep knowledge not only in the domain of metallurgy but also in mechanical and control engineering. These professionals are adept at troubleshooting and optimizing mill operations, seeing them through the lens of both micro and macro-production perspectives. Continuous professional development is encouraged, as the field is ever-evolving with the emergence of newer alloys and industry demands.
cold strip mill
The production environment of cold strip mills speaks volumes of its sophistication.
Located in large industrial complexes, they are operated under stringent safety protocols due to the intense pressures and forces involved in the milling process. The authoritative nature of these operations is underscored by adherence to international quality standards, such as ISO certifications, which assure clients of the uniformity and high-grade quality of the mill's output.
Ownership and maintenance of cold strip mills necessitate unwavering adherence to best practices, as these machines are central to the core operations of industries like automotive, aerospace, and construction. Regular scheduled maintenance, combined with the deployment of advanced diagnostic tools, ensures the longevity and optimal operation of the machinery. Collaboration with industry-leading manufacturers for parts and technical support is common practice, fostering an environment of trust and reliability.
The state-of-the-art technology in cold strip mills is crucial for producing materials that meet the ever-growing demands for sustainable and lightweight solutions. Companies worldwide rely on the cold strip milling process for manufacturing components that can withstand high-stress environments. The materials produced from these mills are integral to innovations in sustainable architecture and fuel-efficient vehicles, backing the global push for enhanced environmental performance.
In conclusion, cold strip mills are not just machines but pillars of technological advancement in modern industrial applications. They synthesize the principles of metallurgy and engineering, driven by expert oversight and authoritative assurance of quality. Trust is built into the very fabric of cold strip mill operations; without it, the bridge to modern innovation and industrial excellence remains incomplete. Whether producing steel sheets for skyscrapers or aluminum for aerospace applications, cold strip mills are at the heart of future-forward metal manufacturing.