Rolling steel and metals have undergone significant advancements since the inception of rolling technology. Among notable innovations, the six high rolling mill stands out for its unique configuration, offering superior precision and efficiency in rolling operations. Unlike traditional mills, which often struggle with maintaining uniform thickness and high precision across broader metals, the six high rolling mill excels in these areas through its distinctive design and technological advancements.
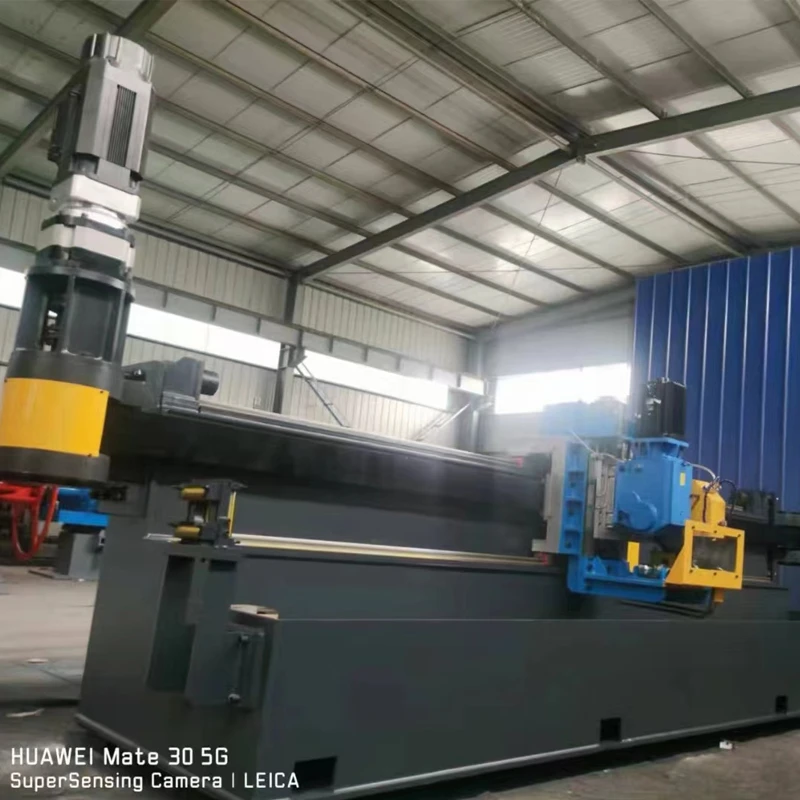
A six high rolling mill operates with a pair of work rolls, two intermediate rolls, and a final pair of back-up rolls. This intricate configuration is pivotal in ensuring the reduction of roll deflections and the improvement of strip thickness consistency. The advanced layout enhances the rolling process’s stability, allowing the mill to maintain optimal pressure and improve product quality, critical for industries demanding precision such as automotive and aerospace sectors.
Precision is a cornerstone of the six high rolling mill's capabilities. Industry experts have long praised its ability to minimize deviations in rolled materials, which is essential in applications requiring strict adherence to specifications. The intermediate rolls in the six high system play a crucial role in correcting any inconsistencies and distribute the pressure applied by the work rolls. This feature results in reduced variations in strip thickness, ensuring that every centimeter of material meets stringent tolerances, a factor that builds significant trust among users reliant on this technology for critical projects.
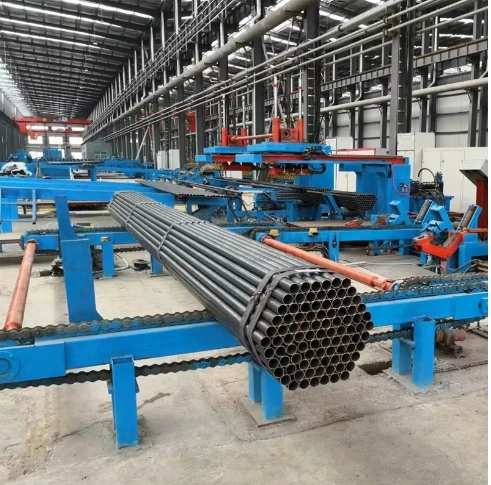
The expertise required to operate a six high rolling mill also attests to its authoritative position within the machinery landscape. Engineers and operators must possess a profound understanding of the mechanical and electrical systems governing the mill’s operations. Only through meticulous training and accumulated experience can operators achieve mastery, underscoring the specialized nature of the technology.
six high rolling mill
Authoritativeness and trustworthiness are further reinforced by the mill’s applications across various industries known for demanding extreme precision and reliability. We see six high rolling mills deployed in steel plants around the world that supply metals for high-stakes industries such as automotive manufacturing, electronics, and aviation. These sectors depend on the continuous research and development efforts that have gone into the design and operation of six high rolling mills, many of which boast innovations geared towards enhancing energy efficiency and reducing operational costs without compromising on quality.
Real-world experiences highlight the six high rolling mill's unparalleled impact. Many steel manufacturers report significant improvements in material quality and production speed after transitioning to this advanced technology. Operators frequently share their success stories and the increased confidence they have in meeting client specifications thanks to the capabilities of the six high mill. Such testimonies enhance the technology’s credibility and build trust among new adopters, establishing the six high rolling mill not just as a piece of equipment but as a linchpin of precision metalwork.
Taken together, the six high rolling mill exemplifies a perfect blend of experience-driven enhancements, professional expertise, and engineering mastery. It holds authority in the field by delivering consistent, high-quality outputs that satisfy the rigorous demands of modern industrial applications. As it stands as a testament to advanced engineering, this mill continues to win the trust of the most demanding steel consumers and sets the benchmark for future innovations in rolling technology.