High-Density Polyethylene (HDPE) is a critical material used in various industries, thanks to its robust characteristics. The manufacturing of HDPE involves sophisticated machinery that demands expertise and precision to produce high-quality outputs. Understanding the machinery used in HDPE manufacturing can significantly enhance production efficiency, reduce costs, and improve the quality of the final product. Below is a comprehensive overview of HDPE manufacturing machines, shedding light on what makes an effective setup.
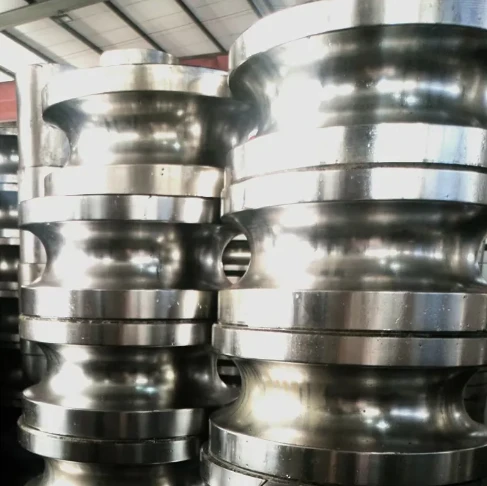
HDPE manufacturing begins with the polymerization process, which transforms ethylene into polyethylene. The machinery involved typically encompasses extruders, blow molding machines, injection molding machines, and rotational molding machines. Each type of machine plays a crucial role, and understanding their nuances is essential.
Extruders are fundamental in the initial phase of turning raw polyethylene into its processed form. This machine heats and forces the material through a die to create a continuous shape as per the product requirements. The efficiency of an extruder is determined by its screw design and speed, heating capabilities, and die configurations. Selecting the right extruder can optimize material consistency and energy consumption, directly affecting the production output's reliability and efficiency.
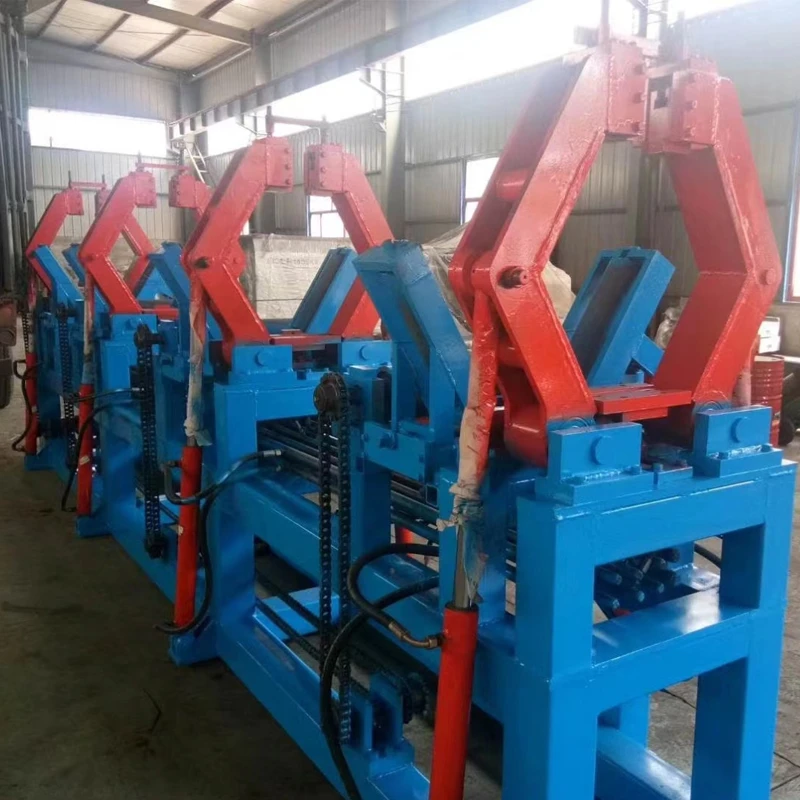
For products such as bottles, containers, and other hollow objects, blow molding machines are used. These machines inflate the molten plastic into the desired shape using air pressure. The versatility of the blow molding machine lies in its ability to produce complex shapes with minimal waste. Core attributes such as mold accuracy, cooling systems, and automation levels distinguish high-performance blow molding machines from the rest. A well-tuned setup ensures uniform wall thickness, an essential parameter in product durability and effectiveness.
Injection molding machines employ a distinct process, injecting molten HDPE into a mold at high pressure. This method is pivotal for manufacturing precise and high-volume parts. Evaluating an injection molding machine involves considering its clamping force, injection speed, and pressure control. These factors influence the machine's ability to produce intricate designs with high repeatability and minimal defects. The machine's automation and integration capabilities with other technologies also enhance production efficiency significantly.
hdpe manufacturing machine
Rotational molding machines present another dimension to HDPE manufacturing, especially for large and hollow products like tanks and playground equipment. These machines allow polyethylene powder to melt and adhere inside a rotating mold. The key to optimizing rotational molding lies in temperature regulation and the rotational speed, dictating material distribution and surface smoothness. Modern machines are equipped with advanced control systems to maintain these parameters, ensuring each product meets exacting quality requirements.
In today’s environmentally conscious world, manufacturers increasingly look for machines that not only offer performance but also sustainability. Modern HDPE manufacturing machinery incorporates features that enable recycling of waste material and reduce emissions. Energy-efficient engines, waste heat recovery systems, and advanced control processes are now integral to top-tier machines. By aligning production processes with sustainable practices, manufacturers can not only enhance their environmental credentials but also realize cost efficiencies in the long run.
Finally, the advancements in IoT and Industry 4.
0 have revolutionized HDPE manufacturing. Smart machines equipped with sensors and data analytics offer real-time performance monitoring and predictive maintenance. These technologies minimize downtime, enhance throughput, and extend the lifespan of machinery, guaranteeing consistent product quality. Manufacturers utilizing these advancements can significantly elevate their operational capabilities, ensuring a competitive edge in the market.
Investing in the right HDPE manufacturing machine is crucial for any business aiming for sustained growth and innovation. By understanding the machinery's features, incorporating sustainable practices, and leveraging technological advancements, companies can optimize their processes and deliver superior HDPE products. The integration of traditional expertise with modern technology stands at the forefront of successful HDPE manufacturing, driving the future of the industry.