Pipe beveling is a critical step in the preparation of pipes for welding and joining. Traditionally, manual methods of beveling were both time-consuming and inconsistent, often leading to quality issues and increased labor costs. Enter the pipe bevel cutting machine—a game-changer in the world of pipe fabrication. These machines are designed to provide consistent, precise, and efficient bevels on pipes of varying diameters and materials, from carbon steel to stainless steel.
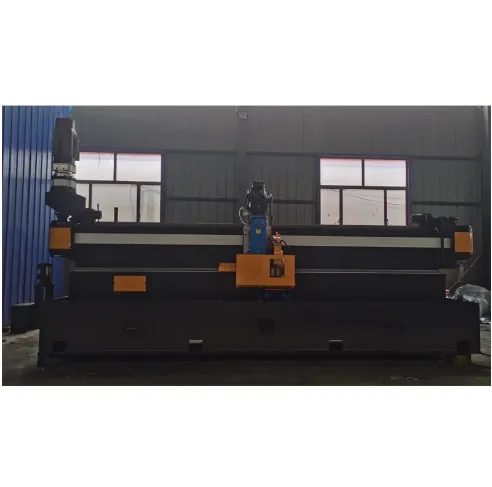
The use of pipe bevel cutting machines enhances operation efficiency significantly. One of the primary benefits is the accuracy achieved with each cut. Unlike manual beveling, which relies heavily on the skill of the operator, these machines leverage advanced technology to ensure that every bevel meets exacting specifications. This not only ensures a snug fit for welding but also enhances the integrity and durability of the connection. Consistent bevels prevent gaps that could jeopardize the welding process, thus minimizing the risk of weld failures that could lead to costly repairs or replacements.
Expert developers of pipe bevel cutting machines emphasize the necessity for robust construction and ergonomic design. High-quality machines are engineered from durable materials that withstand the rigors of heavy industrial usage, ensuring longevity and reducing downtime. Designs focusing on user-friendly interfaces make these machines accessible even for operators who might lack extensive experience. Intuitive controls and clear displays allow for ease of operation, facilitating quick training and reducing the learning curve.
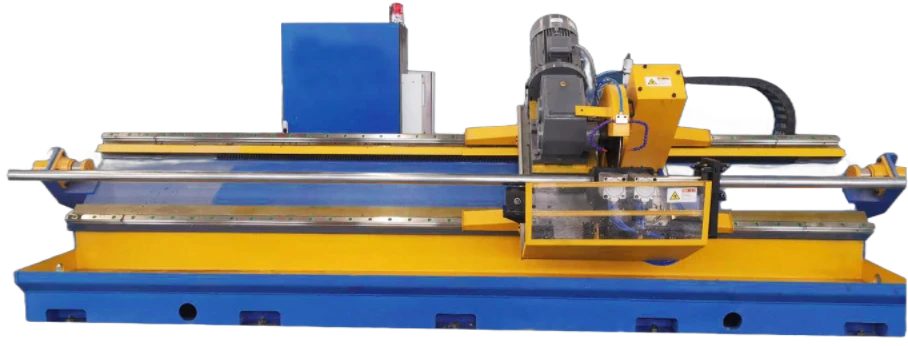
Trustworthiness in a pipe bevel cutting machine is derived from its performance reliability and the support structure surrounding its implementation. Machines from reputable manufacturers show high reliability with minimal mechanical failures, backed by comprehensive warranties that ensure peace of mind for the purchasers. Furthermore, authoritative manufacturers provide stellar after-sale services, including maintenance support and ready availability of replacement parts, which is critical in maintaining seamless operations in busy industrial settings.
pipe bevel cutting machine
When considering a pipe bevel cutting machine, understanding the specific application is vital. Machines vary in capability, with some designed for small-scale operations and others equipped for large, industrial-scale projects. It is crucial to evaluate the machine's compatibility with the types and sizes of pipes regularly used, the frequency of operation, and the specific beveling requirements of the application. Some models offer customizable bevel angles to accommodate various welding specifications, providing flexibility in operations across different projects.
Investing in a machine that integrates well with existing workflows is another crucial factor. The best machines offer versatility, allowing for swift changeovers between different pipe sizes and materials with minimal downtime. This adaptability is essential for operations where multiple projects with varying requirements are ongoing, maximizing efficiency and productivity.
The pipe bevel cutting machine also contributes to safer working environments. By automating what was once a physically demanding manual task, these machines minimize the risk of injury associated with manual handling of tools and pipes. The precision provided reduces the chance of errors that require rework, thereby streamlining processes and enhancing overall safety through consistent and high-quality outputs.
Overall, the adoption of pipe bevel cutting machines represents a strategic enhancement for any operation involved in pipe fabrication and installation. With their ability to deliver precise, consistent bevels while reducing labor costs and improving operational safety, these machines are not only an asset but a necessity in modern industrial applications. Whether for small-scale workshops or large industrial mills, selecting a machine that aligns with specific operational needs and is backed by expert support is crucial for maintaining high standards of production quality and efficiency.