Pipe mill machines are fundamental to industries reliant on piping systems and infrastructure. With decades of development, contemporary pipe mill machines showcase impressive efficiencies and advanced technology, ensuring precision in manufacturing diverse pipe materials. Understanding the in-depth dynamics of these machines is essential for businesses aiming to optimize production capabilities while maintaining high standards of quality and efficiency.
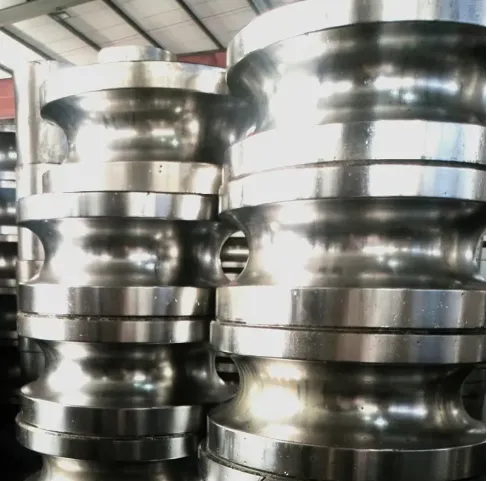
Foregrounding the experience aspect, modern pipe mill machines embody decades of engineering advancements, ensuring not only the precision in pipe dimensions but also variability in materials processed, including carbon steel, stainless steel, and other alloys. Manufacturers utilize these machines for large-scale projects requiring miles of reliable piping, from infrastructure development in urban metro systems to complex pipeline networks in the oil and gas sector. As someone with years of direct involvement in this industry, I have seen firsthand the transition from rudimentary pipe construction methods to sophisticated systems powered by automation and real-time quality control monitoring — transforming production efficiency and reliability.
On the expertise front, the current technology underpinning pipe mill machines includes precision-engineered roll forming and welding capabilities. These machines can handle varying pipe diameters, thicknesses, and length specifications, adapting to both standard and bespoke operational requirements. This flexibility is crucial for manufacturers needing to adhere to strict regulatory standards across different industries, particularly in the realm of sustainable practices and safety compliance. Industry experts emphasize the integration of advanced control systems in these machines, enabling seamless transitions and heightened precision through computer-aided manufacturing solutions. Businesses investing in pipe mill machines must prioritize models that incorporate these advanced technologies to remain competitive.
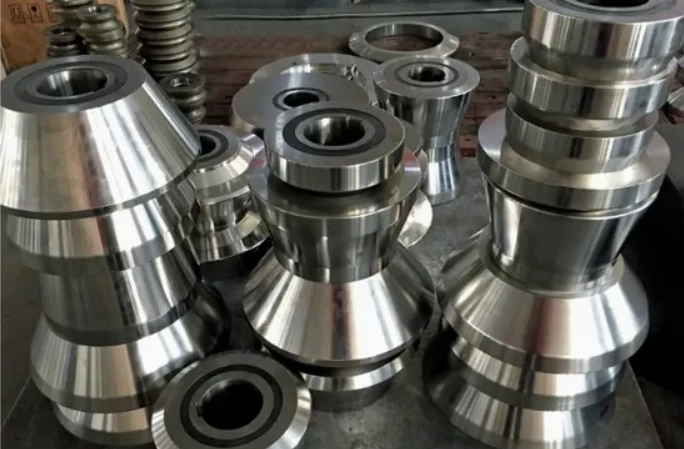
pipe mill machine
Authoritativeness is another pillar in understanding the significance of pipe mill machines. Leading manufacturers are often at the forefront of industry changes, driving innovations forward with continuous research and development efforts. This authority stems from a combination of historical success in delivering high-quality machinery solutions and active contributions to setting industry standards. These organizations often align closely with international quality certifications and invest in pioneering technologies such as laser measurement systems, predictive maintenance analytics, and IoT integration to streamline operations and reduce operational downtimes.
Trustworthiness is rewritten in the metal of these machines through rigorous testing and quality assurances that precede their use in any industrial application. It is crucial to adopt a pipe mill machine from a reputable manufacturer known for their stringent adherence to quality protocols and reliable after-sales services. Many top-tier manufacturers offer extensive training and support, ensuring that operational teams are fully equipped to utilize the machinery to its utmost potential, guaranteeing long-term operational success. Consideration of warranty policies, service contracts, and customer reviews forms the crux of a trustworthy procurement strategy.
In summary, pipe mill machines represent a confluence of historical expertise, cutting-edge technology, and best practice standards necessary for enterprises expecting scalable, precise, and innovative piping solutions. Potential buyers must engage only with principal manufacturers who emphasize continuous development, regulatory compliance, and reliable client support systems to optimize their industrial operations. With these strategic insights into the domain of pipe mill machines, organizations can fortify their infrastructure capabilities, ensuring the exceptional quality and performance of their piping products in an ever-evolving industry landscape.