Roll forming stands as a pivotal process in the manufacturing industry, providing unrivaled precision and efficiency for creating consistent cross-sectional metal profiles. As one delves deeper into the world of roll forming manufacturers, it becomes evident that their role is crucial in pushing the boundaries of what’s possible in metal shaping.
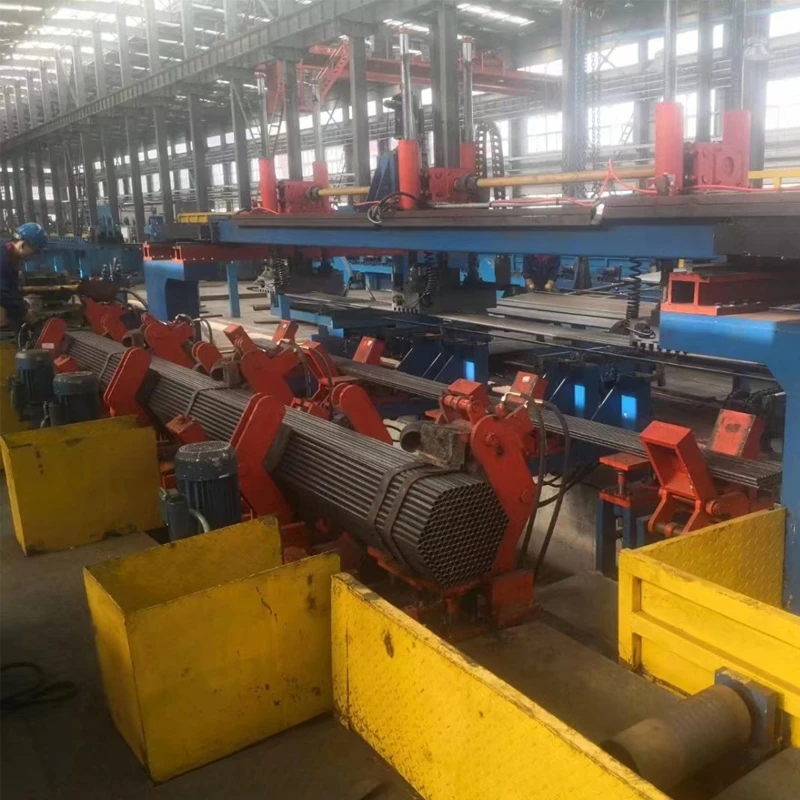
At the heart of roll forming lies an experience-driven technique, honed over decades of advancements and innovations. This method involves passing a long strip of sheet metal, typically coiled steel, through sets of rolls mounted on consecutively arranged stands. Each set of rolls performs incremental portions of the bend, until the desired cross-section profile is achieved. This progressive approach not only renders roll forming extremely efficient but offers manufacturers the ability to produce high-volume metal components with remarkable consistency and minimal waste.
In the realm of expertise, roll forming manufacturers boast proficiency in material science and engineering, understanding how different metals react under specific conditions of pressure and temperature. Manufacturers use a variety of materials, from galvanized steel to aluminum, each with its distinct properties and applications. By leveraging cutting-edge CAD/CAM software for designing precise roll profiles and employing advanced roll forming machines, these professionals ensure that the end products meet stringent quality and performance standards.
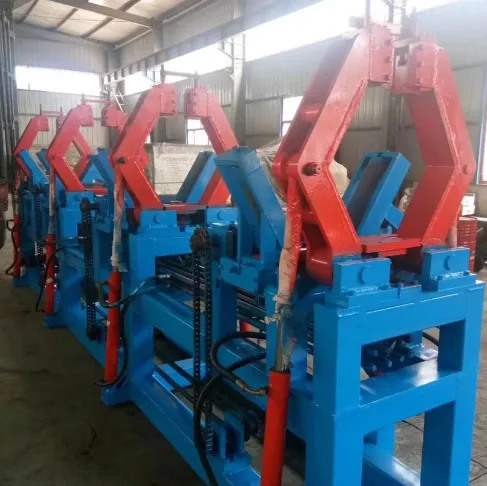
Authority in the roll forming sector is often derived from a manufacturer’s track record, reputation, and the certifications they hold, such as the ISO 9001 for quality management systems. Many of these manufacturers work collaboratively with diverse industries—including automotive, construction, and electronics—to deliver bespoke solutions tailored to specific needs. Whether it’s the automotive industry’s demand for aerodynamic profiles or the construction sector’s requirement for durable, weather-resistant components, roll forming manufacturers can deliver with precision.
roll forming manufacturers
Trustworthiness in this field emanates from a transparent process where manufacturers maintain an open dialogue with clients. By providing detailed insights into the production process, material selection, and quality assurance protocols, roll forming manufacturers build confidence with their clients. The importance of trust is elevated when considering the critical applications these metal components serve—from safety components in vehicles to structural supports in buildings—necessitating an unwavering guarantee of reliability.
Roll forming manufacturers continue to innovate, adopting sustainable practices to reduce environmental impact. Many are investing in solar energy systems to power their operations and implementing recycling programs to handle scrap metal efficiently. Moreover, advancements in automation and AI are enhancing process efficiency, reducing lead times and production costs, and allowing manufacturers to offer competitive pricing to their customers.
In conclusion, roll forming manufacturers represent the confluence of experience, expertise, authority, and trustworthiness. Their ability to deliver high-quality, precise, and reliable metal components makes them indispensable partners across industries. As they continue to push the technological envelope while adhering to best practices, these manufacturers will undoubtedly remain at the forefront of the manufacturing landscape, shaping the future of metal production with skill and integrity.