Rolling shutter forming machines have revolutionized the manufacturing industry, offering precision, efficiency, and versatility in producing roll-up doors, shutters, and similar products. These machines, pivotal for manufacturers, leverage advanced technology to meet the growing demands for customized and durable solutions in various sectors, including industrial, commercial, and residential applications.
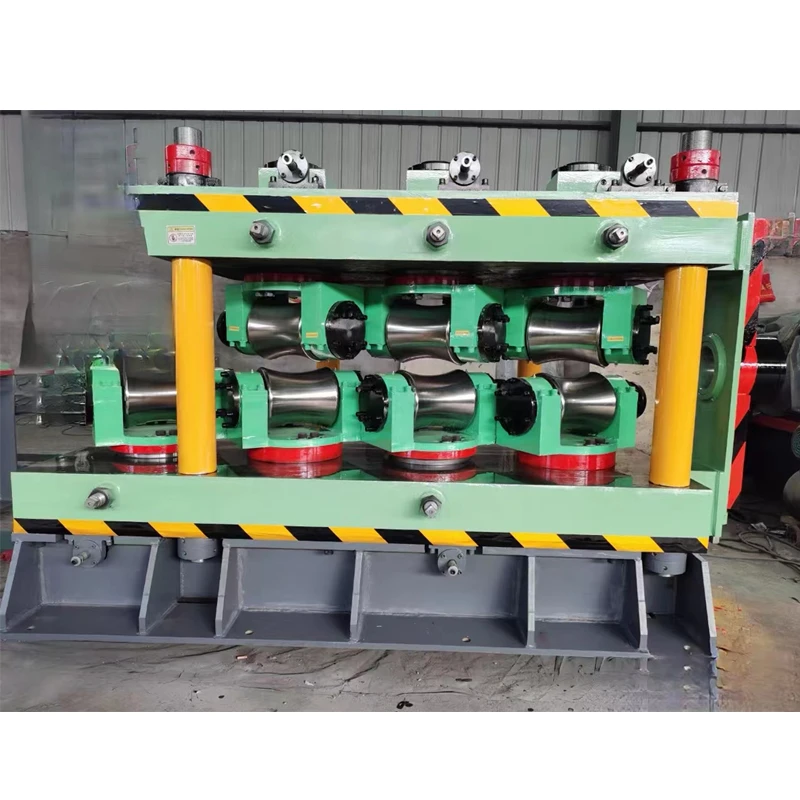
Engaging with the rolling shutter forming machine starts with understanding its core components and functionalities. At the heart of its operation is the roll forming process, a continuous bending technique in which long strips of metal, typically coiled steel, pass through sets of rolls to achieve a desired cross-section. This method is not only fast but also ensures uniformity across large quantities of product, which is crucial for maintaining high standards in production lines.
A critical factor distinguishing premium rolling shutter forming machines is their adaptability to diverse material types and thicknesses. Whether working with aluminum, stainless steel, or galvanized materials, these machines offer customizable settings that allow for precise adjustments. This feature is indispensable for manufacturers who need to cater to various client specifications without compromising on quality or efficiency.
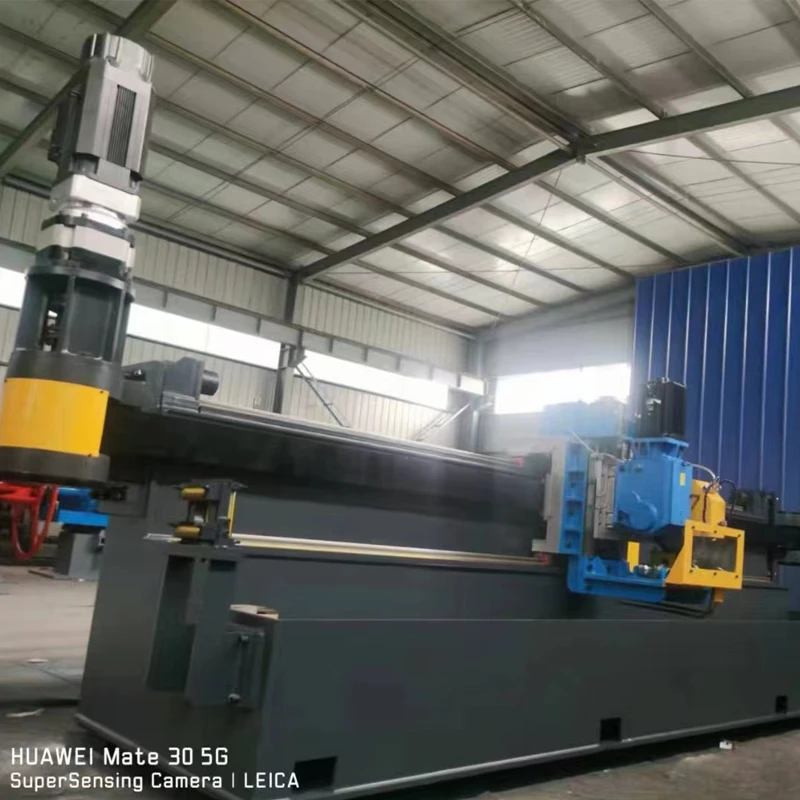
The expertise involved in operating a rolling shutter forming machine cannot be understated. Operators need a deep understanding of both the mechanical and digital aspects of these machines. Modern iterations are equipped with user-friendly interfaces, often incorporating touchscreens and digital controls that enable quick modifications and reduce setup times. Automated features like these not only enhance productivity but also contribute significantly to minimizing human error, which can be costly in high-volume production.
Authoritativeness in this field comes from manufacturers who have established themselves through rigorous testing and innovation. Companies that produce rolling shutter forming machines often engage in constant research and development, aiming to refine their technology and uphold a reputation for reliability and excellence. Clients should seek out manufacturers with proven track records, evidenced by certifications and client testimonials, which are vital indicators of trustworthiness in this competitive market.
rolling shutter forming machine
Further underscoring the trust factor is the after-sales support and services provided by the manufacturers or dealers. Comprehensive training programs for operators, timely maintenance services, and the availability of replacement parts are essential elements that significantly impact the longevity and performance of the rolling shutter forming machine. Manufacturers who offer robust support systems typically foster greater client satisfaction and long-term relationships, contributing to their esteem in the industry.
From a sustainability perspective, rolling shutter forming machines contribute to reducing waste substantially. By using precise forming methods and optimizing material usage, these machines align with eco-friendly practices that more businesses are adopting today. Efficiency translates into fewer raw materials required and lower energy consumption, marking an important step towards sustainable manufacturing processes.
Real-world experiences from businesses utilizing rolling shutter forming machines further solidify their value. Anecdotal evidence from industry professionals highlights increased production capabilities and improved lead times, validating these machines as essential investments for modern manufacturing hubs. Companies often report a noticeable boost in product quality and consistency after integrating these machines, showcasing their capability to meet rigorous standards and diverse design requirements.
In summary, the rolling shutter forming machine is an indispensable tool in modern manufacturing, combining advanced technology with precision engineering. Manufacturers and operators who harness the full potential of these machines not only streamline their production processes but also reinforce their position in a competitive market. The continuous evolution of roll forming technology promises even greater advancements, setting benchmarks for efficiency, quality, and sustainability in the years to come.