High frequency welded tubes (HFW tubes) represent a pivotal evolution in the realm of industrial piping and structural applications. These tubes, known for their precise engineering and versatility, are manufactured through a high frequency electric current, which fuses the edges of rolled strips together, creating a seamless and robust bond.
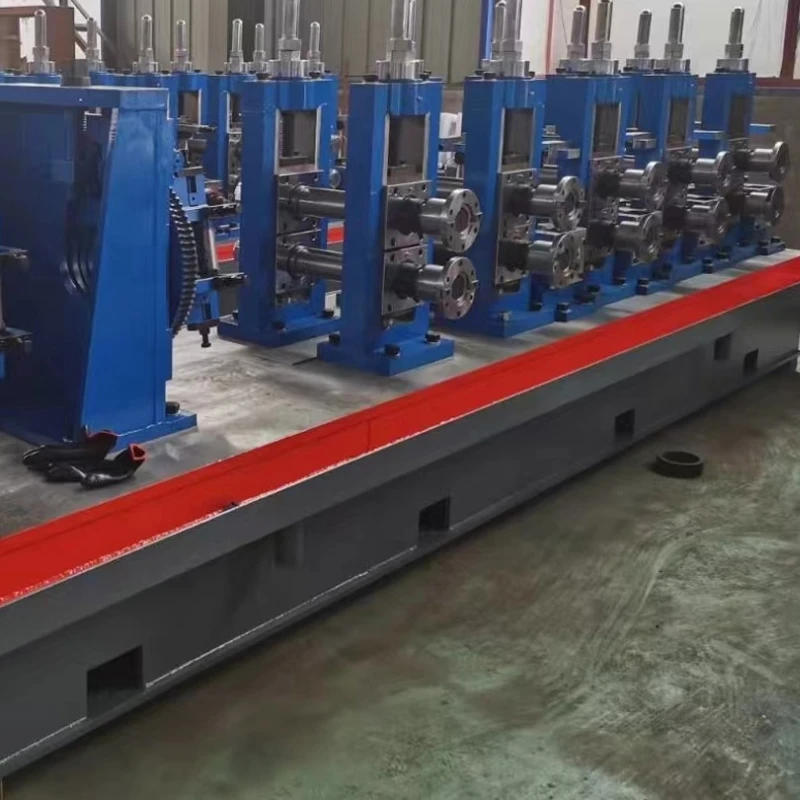
In the industrial sectors where efficiency and reliability are paramount, HFW tubes have emerged as a front-runner. Their significance lies not just in their production, but in their extensive application, which spans industries such as oil and gas, construction, automotive, and beyond. The high frequency welding process enhances the mechanical properties of the tubes, resulting in improved strength and ductility, which are critical in withstanding harsh operating environments.
From an expert's perspective, the technology behind high frequency welded tubes offers versatility and customization. These tubes can be tailored to specific requirements, allowing for variations in diameter, thickness, and materials. This adaptability enables industries to use HFW tubes for a multitude of purposes, including not only load-bearing structures but also intricate automotive components. The precision of the welding process ensures that the tubes maintain integrity under pressure, which is why they're often employed in critical applications such as pipelines and infrastructure projects.
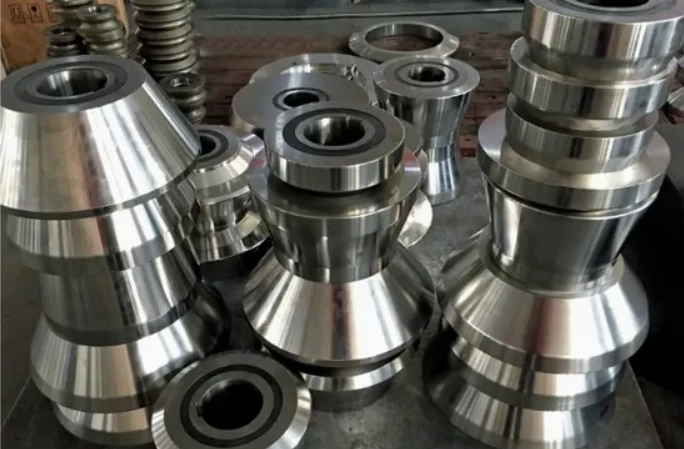
Authoritativeness in manufacturing is achieved through stringent quality control measures and the adoption of international standards. Manufacturers of high frequency welded tubes often hold certifications from recognized bodies, ensuring that their products meet or exceed industry benchmarks. This commitment to quality is reflected in the durability and performance of the tubes, further establishing the reliability of HFW technology.
high frequency welded tube
Trustworthiness is another cornerstone of high frequency welded tubes. The welding process itself is conducted under controlled conditions, minimizing the risk of defects and ensuring consistent production quality. Suppliers often provide detailed documentation and traceability of the materials used in the production process, offering transparency and confidence to their clients.
Real-world applications also testify to the dependability of HFW tubes. In the construction of skyscrapers, for example, these tubes provide foundational support, balancing the demands of weight and flexibility, which are crucial for standing against natural forces. In the realm of oil and gas, high frequency welded pipelines transport resources over vast distances, proving their resilience to corrosive environments and operational stresses.
Expertise in this field extends to understanding the nuances of when and where to employ HFW tubes. Engineers and project managers rely on specific data and historical performance metrics to select the appropriate tube specifications, ensuring that projects are executed with precision and efficiency. The continuous research and development in welding technologies also mean that HFW tubes are continually being improved, incorporating advancements in metallurgy and manufacturing techniques.
In conclusion, high frequency welded tubes not only exemplify technological innovation but also embody the principles of experience, expertise, authoritativeness, and trustworthiness. Their multifaceted application in diverse industries highlights their indispensability and underscores the importance of choosing a reputable manufacturer for optimal performance and longevity. With ongoing advancements and strict adherence to quality standards, HFW tubes will undoubtedly remain integral to industrial and structural advancements globally.