High-frequency welded pipes (HFW pipes) are a type of industrious craftsmanship that assimilate advanced technology and meticulous engineering to enhance manufacturing processes. These pipes are predominantly employed across various sectors, including construction, automotive, and oil & gas, due to their exceptional durability and versatility. The secret to their robustness lies in the unique welding process used, which distinguishes HFW pipes from others.
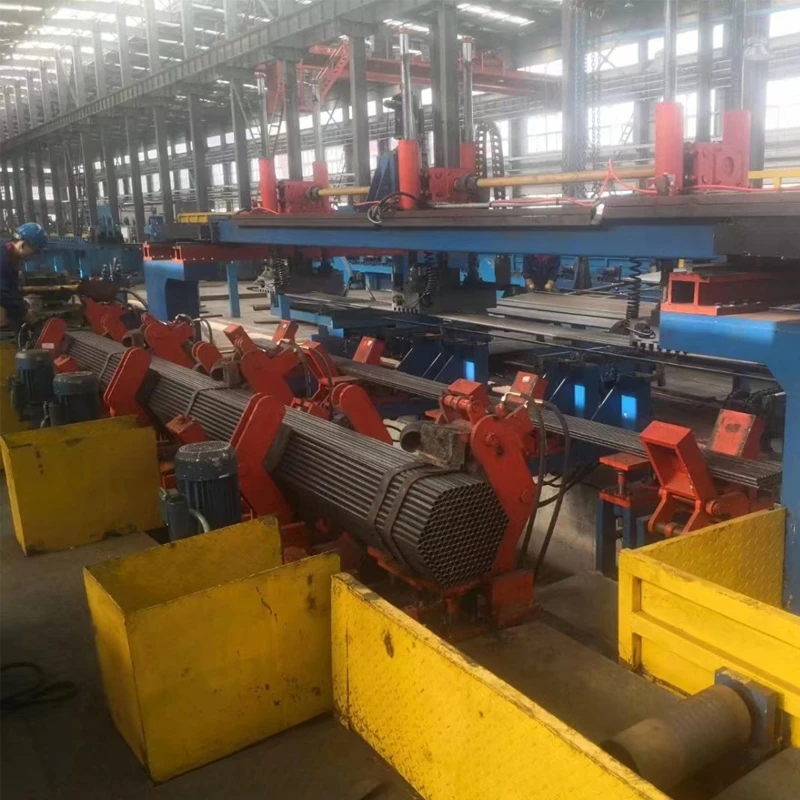
The process of manufacturing high-frequency welded pipes involves high-frequency resistance welding. This technique exploits the ability of high-frequency electrical currents to generate heat and join materials. The metal edges to be welded are heated using an electrical current and then forced together, resulting in a seam that exhibits strength equivalent to, or even exceeding that of the base metal. This method ensures minimal thermal distortion, maintaining the integrity and straightness of the pipe.
Experience in utilizing HFW pipes reveals their efficiency and integrity in demanding applications. Users and manufacturers often laud these pipes for their superior mechanical properties, including high tensile strength, excellent impact resistance, and the ability to withstand harsh environmental conditions. Their lightweight nature compared to seamless pipes is another attractive attribute, as it translates to reduced transportation costs and easier handling.
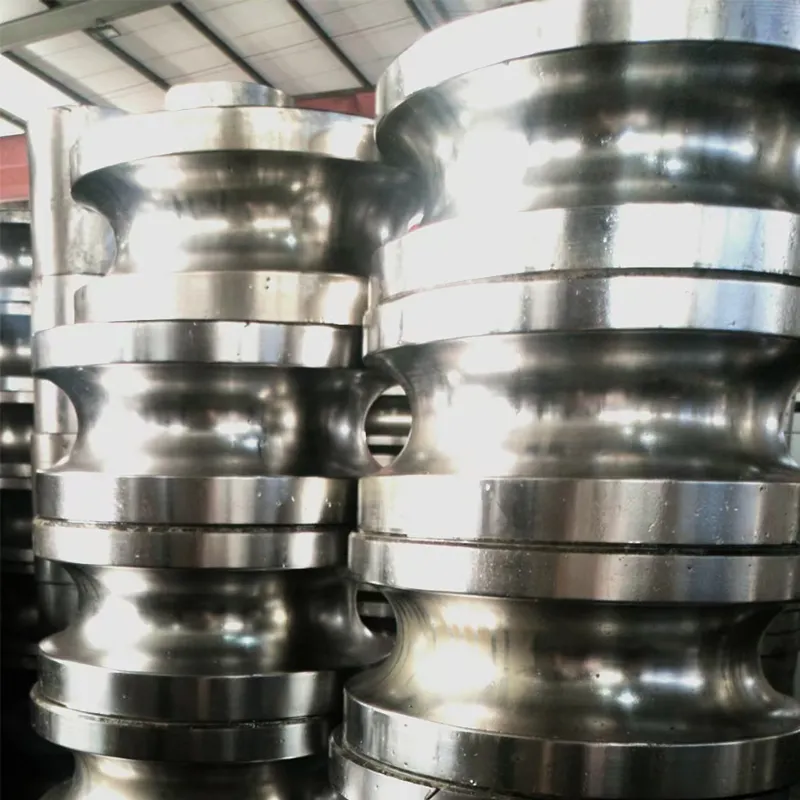
The expert consensus is that the precision in HFW pipe production enables these pipes to meet strict international standards. Manufacturing facilities are often equipped with state-of-the-art technology that allows for precise monitoring and control over the welding processes. This ensures product uniformity, which is crucial for installations requiring exact specifications. Furthermore, manufacturers often conduct rigorous quality control measures, including ultrasonic testing and hydrostatic testing, to ensure each pipe meets the necessary performance criteria.
high frequency welded pipe
Authoritative insights highlight the fact that high-frequency welded pipes play a pivotal role in infrastructure development. HFW pipes' ability to reliably transport fluids and gases over long distances without leakage makes them indispensable in the pipeline industry. Moreover, their resistance to corrosion extends their service life, contributing to the infrastructure's longevity. In construction, these pipes serve as structural supports, owing to their capacity to endure heavy loads and stress.
In terms of trustworthiness, HFW pipes have established a strong reputation over the years. Engineers and project managers trust them for critical applications due to their robust construction and proven track record. Many industries rely on certificates and third-party verifications to ensure compliance with safety standards, which adds an additional layer of trust.
In conclusion, high-frequency welded pipes embody a harmonious blend of expert engineering and reliable performance. Their innovative production process and adherence to stringent quality standards make them a preferred choice across various industries. Companies leveraging these pipes benefit from their strength, durability, and cost-efficiency, ultimately ensuring they meet both operational demands and economic targets. The ongoing development and application of HFW pipe technology continue to underscore its critical role in modern industrial applications, reinforcing its reputation as a top-tier piping solution.