In the world of metal fabrication, the shear press brake is an indispensable tool that expertly merges precision with versatility, making it a cornerstone for any modern workshop. As seasoned professionals in the field, we comprehend the immense value these machines bring to manufacturing projects, from small-scale artisanal endeavors to large industrial productions.
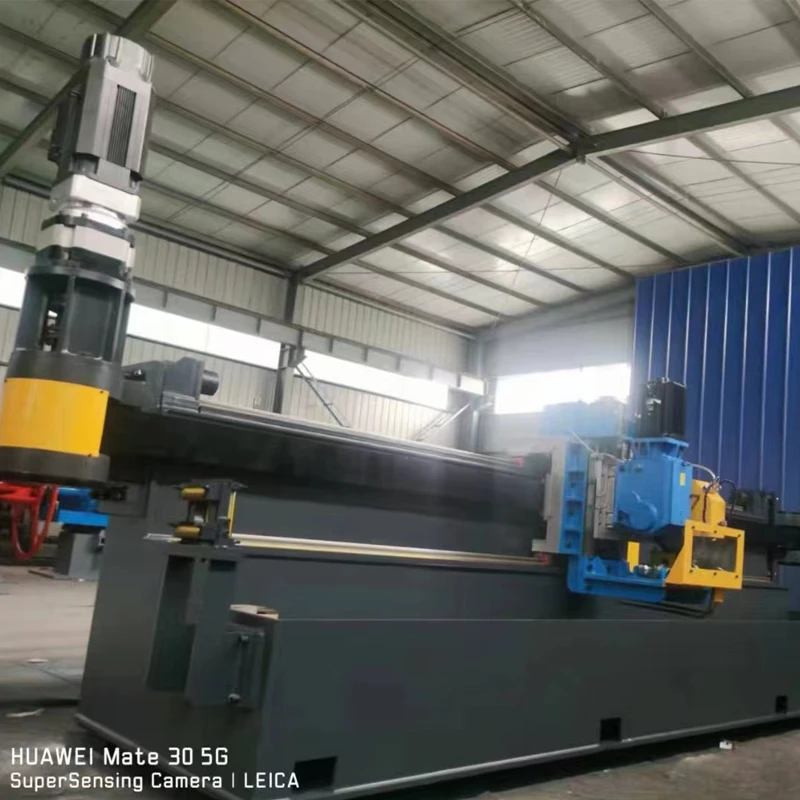
Understanding the nuances between different types of shear press brakes allows you to maximize efficiency in metal bending and shearing operations. These machines are celebrated for their ability to achieve intricate bends with exceptional accuracy thanks to their advanced technological integrations.
This makes them suitable for producing complex components required in industries such as automotive, aerospace, and construction.
One of the key aspects that set shear press brakes apart is their precision in cutting metal sheets to exact specifications. The shearing process involves the delicate balance of applying optimal force to cleanly separate material without distorting the integrity of the metal. Expert operators recognize that maintaining sharp, robust blades and regular calibration is crucial for prolonging machine lifespan and securing high-quality output. Precision in these operations not only ensures aesthetic appeal but also enhances structural reliability, making parts suitable for the most demanding applications.
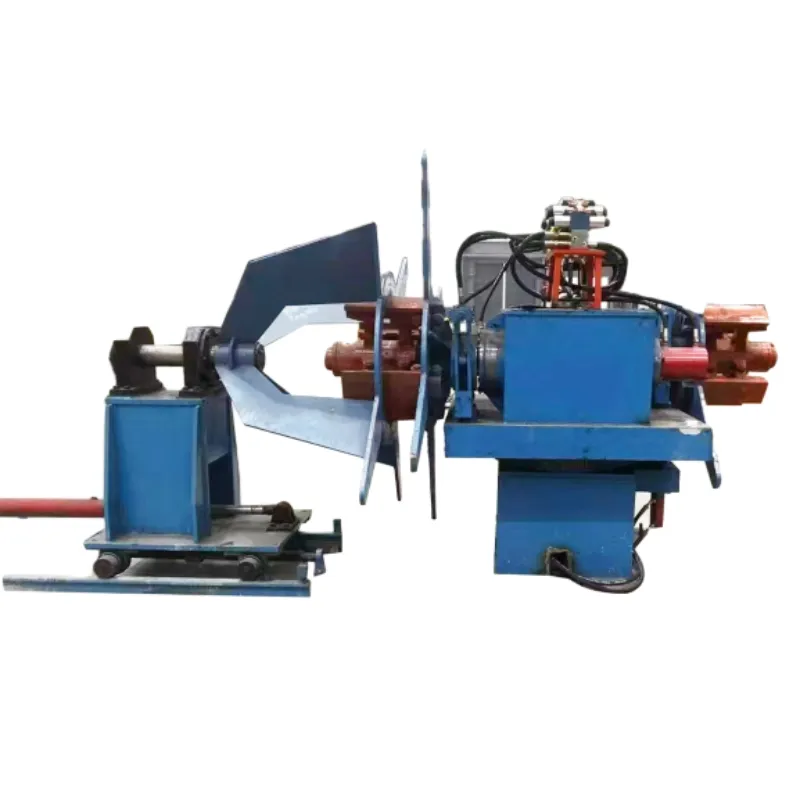
Our experience emphasizes that choosing the right shear press brake involves careful consideration of several factors. First, the size and volume of the production dictate whether a hydraulic, mechanical, or servo-electric model is the most suited for the task at hand. Hydraulic models, known for their power, are ideal for heavy-duty applications, while mechanical models offer speed and efficiency for lighter materials. Servo-electric machines, on the other hand, are growing in popularity due to their energy efficiency and reduced maintenance needs.
Expertise in employing shear press brakes also involves understanding the importance of material properties and machine configuration. Operators must be adept in configuring the punch and die according to the material's thickness, tensile strength, and bend radius. Mastery over the choice and setup of tooling increases the machine's effectiveness and reduces the risk of errors or rework, which is critical in maintaining workflow efficiency and minimizing waste.
shear press brake
Shear press brake technology continually evolves, with modern models incorporating sophisticated computer numerical control (CNC) systems. These advancements not only enhance precision but also streamline operations through user-friendly interfaces that store design configurations for quick recall. The integration of CNC technology represents a leap in ensuring repeatability and reducing operator fatigue, allowing for complex projects to be completed with greater ease.
Authoritativeness in metalworking extends beyond hands-on operation to include a constant engagement with industry developments. Our trusted partners often highlight the importance of staying informed through professional networks, symposia, and certification programs. These channels reinforce not only the technical knowledge necessary for optimal use but also provide insights into emerging materials and techniques that can be leveraged for competitive advantage.
Trustworthiness is built over time and proven through consistent delivery of quality work. Customers know they can depend on workshops that utilize shear press brakes for their durability and precision. By investing in continuous training and maintaining open communication channels with clients, fabricators can foster long-term relationships grounded in reliability and mutual respect. Confidence in our equipment and processes translates to trust from our clientele, reinforcing our position as leaders in the metalworking domain.
In the pursuit of excellence, the shear press brake stands as a testament to innovation and craftsmanship in metal fabrication. Its versatility caters to a wide range of applications, and with knowledgeable professionals at the helm, these machines bring both creativity and precision to the forefront of production capabilities. Whether you're producing intricate designs requiring meticulous attention to detail or robust components engineered for strength and durability, shear press brakes continue to be an indispensable ally in crafting the future of metalworks.