The integral role that shear press brakes and slip rolls play in modern fabrication processes cannot be overstated. As essential tools in metal and sheet fabrication, their utility spans numerous industries, including automotive, aerospace, and manufacturing. Understanding their functionality and the nuances of their operation can empower businesses to maximize efficiency and precision in their production processes.
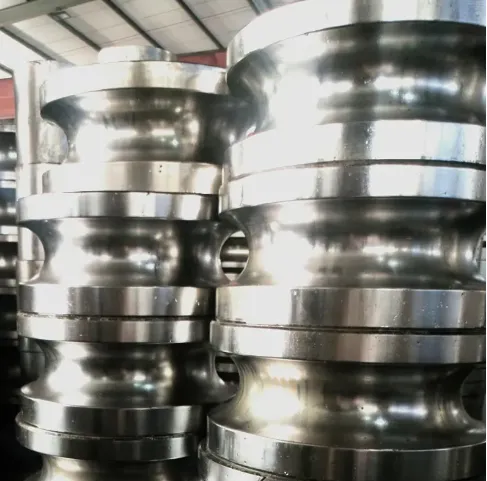
Shear press brakes are indispensable in the shaping and bending of sheet metal. A press brake is renowned for its ability to produce precise bends and folds in varied materials through a forceful downward thrust. The mechanics involve positioning metal sheets over a die, where an upper punch applies pressure to achieve the desired angle or fold. This process necessitates a profound understanding of both the material at hand and the machine's calibration to ensure consistency and accuracy in the resultant products.
Key to maximizing the utility of shear press brakes is the selection of appropriate tooling. It's imperative to understand the relationship between the thickness of the material, the radiation, and the press brake tonnage. Choosing the correct punch and die is vital to avoid unnecessary wear on equipment, ensuring longevity and cost-effectiveness. A well-maintained press brake, equipped with the correct tools, is an asset that enhances production capabilities, minimizes waste, and reduces downtime.
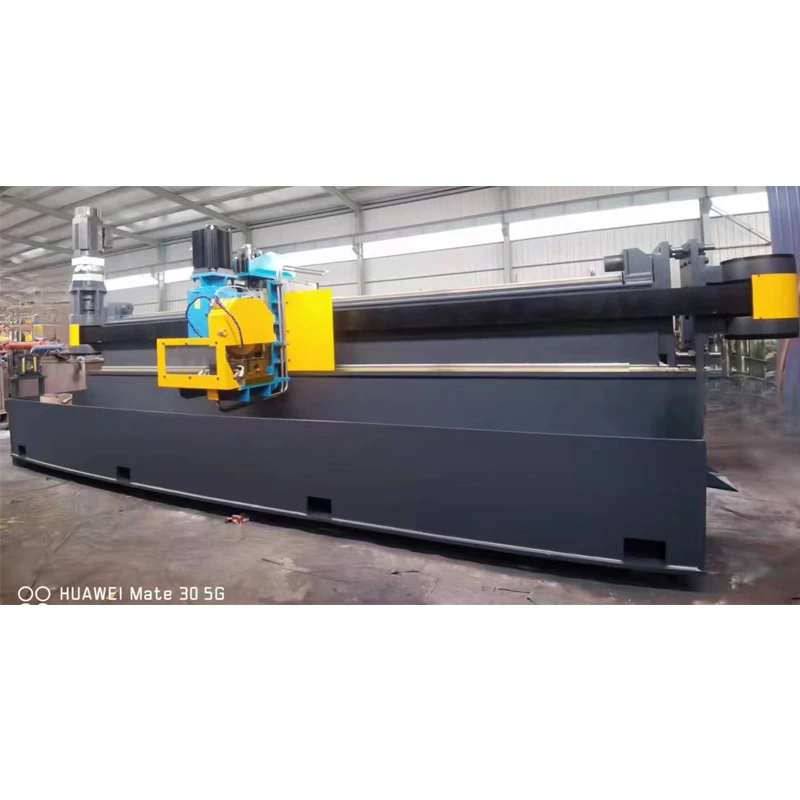
Slip rolls, often called plate rolls, function to create curves and cylindrical formations in metal sheets. The slip roll comprises three rollers, with the positioning of the material ensuring a gradual formation of the desired shape as it's processed through the rollers. Proficiency in managing the tension and position of the rollers is critical to achieve smooth, precise curves without compromising the integrity of the material.
For operators of slip rolls, the importance of proper training cannot be overstated. Navigating the nuances of metal thickness and diameter of the rolls is essential. Recognizing the stress limits of materials prevents overstretching, which can lead to warping or cracking. Expertise in slip rolling involves a balance of fine-tuning roller positions and understanding the material's properties to ensure uniformity in roll formation.
shear press brake and slip roll
A significant aspect contributing to the authority and trustworthiness in the use of shear press brakes and slip rolls is adherence to safety protocols. Both machines involve large amounts of pressure and the movement of heavy materials, making safety vigilance indispensable. Equipment should always be operated by trained professionals who are well-versed in safety standards such as those set forth by organizations like the Occupational Safety and Health Administration (OSHA).
To foster trustworthiness and reliability, maintaining an organized maintenance and inspection schedule is critical. Regular checks for alignment, lubrication, and wear and tear not only prolong machine life but also ensure production is not hampered by unexpected equipment failures. Additionally, the integration of modern technology, such as CNC systems in press brakes, augments precision, allowing for programmable cuts and folds — further enhancing production capabilities.
In terms of experience, businesses that have integrated shear press brakes and slip rolls into their operations often report enhanced flexibility in product design and production efficiency. By combining these tools with proficient operators, businesses can achieve a diverse array of metal fabrication outcomes with high precision and repeatability.
Moreover, sourcing high-quality materials and maintaining a meticulous inventory system ensures that the production process remains unhindered. By understanding material compatibility and machine capabilities, operators can produce high-quality outputs that meet industry standards and specific client needs.
Investing in shear press brakes and slip rolls is a strategic decision, one that promises returns not only in productivity but also in the ability to deliver bespoke products with precision. As industry demands continue to grow, so does the need for expertise in handling these machines. Continuous learning and adaptation to new technologies will keep operators at the forefront of metal fabrication, ensuring they remain competitive in an ever-evolving market landscape.