Professional expertise and experience are crucial when exploring the intricate world of shear press brake slip rolls. As technology evolves, so do the methods and machines manufacturers use to shape and form metal. The following insights delve into the use and importance of these manufacturing tools, providing a comprehensive understanding for industry professionals.
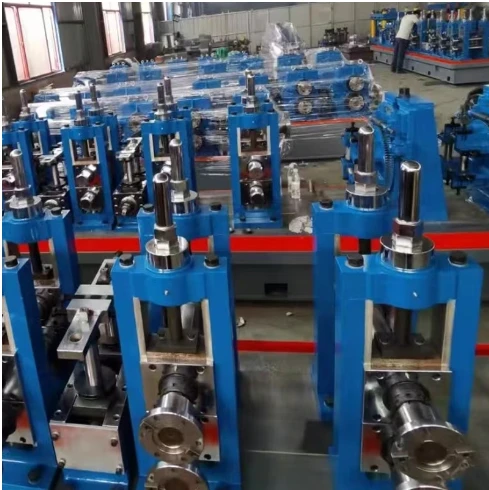
Shear press brake slip rolls are used extensively in metal fabrication, each playing a critical role in shaping materials for various applications. These machines are indispensable for creating components with precision and efficiency, essential for sectors such as automotive, aerospace, and heavy machinery. Their ability to produce consistent and accurate bends or rolls makes them a cornerstone in any professional metal shop.
Shearing machines are designed to cut metal sheets into specific dimensions. This precision cutting is a pivotal first step in any fabrication process. The shearing process involves a blade that descends onto a fixed blade, slowly applying pressure until the metal yields and separates. Professionals appreciate the simplicity and effectiveness of shearing, which minimizes downtime and maximizes productivity. Moreover, modern shearing machines often incorporate advanced technologies such as CNC controls, which enhance efficiency and reduce human error.
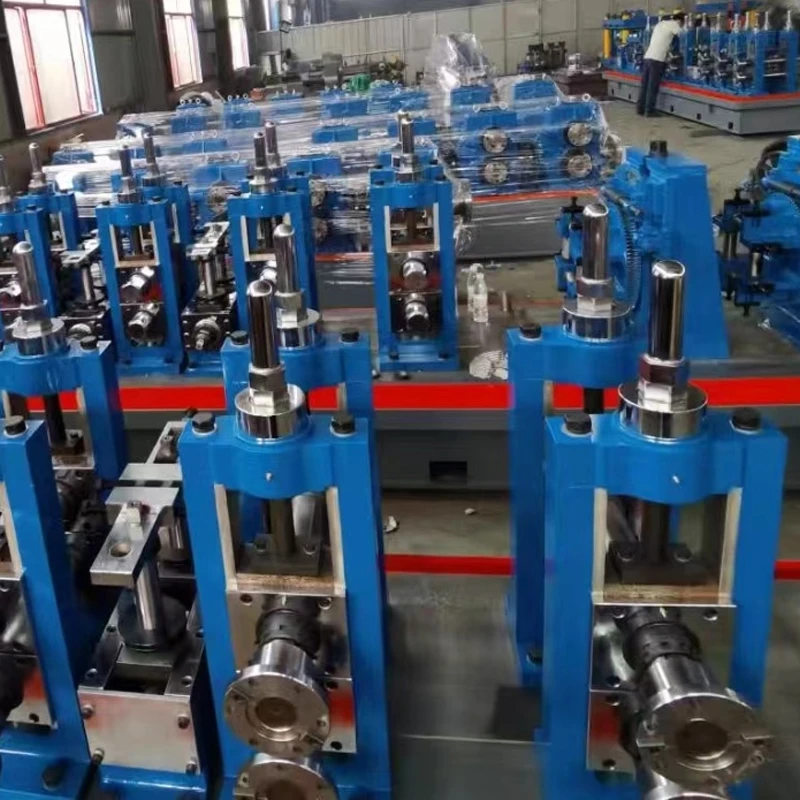
Once the metal is trimmed to size,
press brakes take center stage. These machines are used for bending sheet metal into predetermined angles. The most common configurations include air bending, bottom bending, and coining, each method offering various advantages in terms of precision and tool wear. A press brake works by clamping the metal sheet between a punch and die, applying calculated force to achieve the desired bend.
In the metal fabrication industry, the expertise on press brakes extends beyond basic operation. Knowledge about machine tonnage, bending lengths, and die selection is vital in producing accurate components without damaging materials. Modern press brakes come equipped with features like variable tonnage and programmable back gauges. Such innovations have improved the machinist's ability to perform complex bends efficiently.
shear press brake slip roll
Slip rolls, often seen as the final piece of the trifecta, are essential for rolling sheet metal into cylindrical shapes. These machines are indispensable for creating pipes, cones, and other rounded parts. Slip rolls operate by passing sheet metal through a set of adjustable, rotating cylinders, gradually molding the material into shape. For a fabricator, understanding the nuances of roller adjustment, material thickness, and the rolling process's timing is crucial for maintaining consistency and precision.
Shear press brake slip rolls represent an area in metal fabrication where professional knowledge directly correlates with workplace efficiency. Seasoned operators not only keep up with technological advancements but are also adept at troubleshooting and maintaining these machines, ensuring longevity and consistent output.
From a trustworthiness perspective, manufacturers and suppliers that provide detailed specifications and transparent information about these machines empower buyers to make informed decisions. It is essential to offer training and continuous support to ensure operators stay cutting-edge in their skills and safety. Warranty provisions and service agreements further enhance trust, as they are indicative of a manufacturer's confidence in the durability and reliability of their products.
In closing, the integration and mastery of shear press brake slip rolls are critical components in metal fabrication. Their combined use leads to enhanced productivity, precision, and efficiency—profoundly impacting the quality of the final product. In a rapidly evolving industry, having a robust understanding of these machines provides professionals with a competitive edge, affirming their expertise and establishing authority in the field. As fabrication technology advances, staying informed and skilled with these tools not only solidifies trust with clients but secures a shop's reputation for excellence.