Tandem mills are a pivotal component in the cold rolling process of metals, offering an ability to improve efficiency, precision, and overall production quality. Here is an in-depth exploration of tandem mill cold rolling, highlighting essential aspects that should captivate manufacturers and stakeholders interested in optimizing their metal fabrication processes.
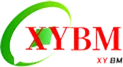
Tandem mill cold rolling, predominantly used in the steel and aluminum industries, involves employing several mill stands in a sequence to compress metal sheets. Each stand incrementally reduces the thickness of the material until the desired specification is achieved. This setup delivers a higher throughput and can significantly enhance product quality, making it an indispensable part of modern manufacturing.
Experience is key when evaluating tandem mill cold rolling systems. Operators often note that the initial setup phase is critical, as achieving the precise alignment of rolls ensures uniform thickness and surface finish. Misalignment can lead to inconsistent results and increased wear on the equipment. As such, seasoned operators understand the importance of regular maintenance and alignment checks to maintain optimal performance.
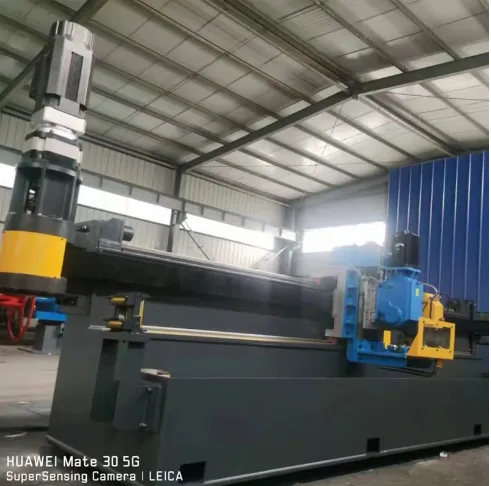
From an expertise perspective, the cold rolling process through tandem mills is notable for its ability to produce thinner gauge products more efficiently than other methods. The process increases material strength via strain hardening, enhancing properties such as tensile strength and durability without necessitating additional heat treatments. This is particularly beneficial for industries like automotive, where both material strength and lightweight characteristics are paramount.
Authoritativeness in the realm of tandem mill cold rolling can be seen in the technological advancements and machinery innovations that continually improve production capabilities.
Modern tandem mills are equipped with computerized control systems that provide real-time monitoring and adjustments. These systems ensure precision and consistency across production runs, offering insights that only experts with a deep understanding of the machinery could fully optimize.
tandem mill cold rolling
Trustworthiness is reinforced by the environmental benefits associated with tandem mill cold rolling. Unlike hot rolling, which requires a significant amount of energy to heat metals to a high temperature, cold rolling operates at room temperature, reducing energy consumption and associated emissions. Manufacturers who prioritize environmentally sustainable operations should consider integrating or upgrading their tandem rolling mills to bolster their green credentials.
The economic advantages of tandem mill cold rolling cannot be overstated. By utilizing this method, factory throughput can be maximized, and scrap rates minimized, leading to a more efficient operational workflow. The material savings often offset the initial costs associated with implementing tandem mills, and over time, they contribute substantially to the bottom line. Businesses looking to sharpen their competitive edge should consider investing in tandem mills to achieve long-term cost efficiency.
Moreover, the flexibility offered by tandem mill cold rolling is significant. It accommodates a diverse range of alloys and thicknesses, allowing manufacturers to adapt to market demands swiftly. This adaptability ensures that companies can remain responsive to changes in consumer requirements, a crucial factor in maintaining relevancy and competitive advantage in the marketplace.
In conclusion, the strategic implementation of tandem mill cold rolling systems presents a compelling case for manufacturers seeking to elevate their production capabilities. Through enhanced efficiency, product quality, and environmental responsibility, tandem mills address the necessity for modern manufacturing solutions that are both economically viable and environmentally sound. As industries continue to evolve, those equipped with advanced knowledge and tools will undoubtedly lead the charge towards greater innovation and productivity in metal fabrication.